The Evolution, Impact of Automation in Electrical Manufacturing
The Evolution, Impact of Automation in Electrical Manufacturing
Explore how AI and other technologies are affecting efficiency, quality, and safety
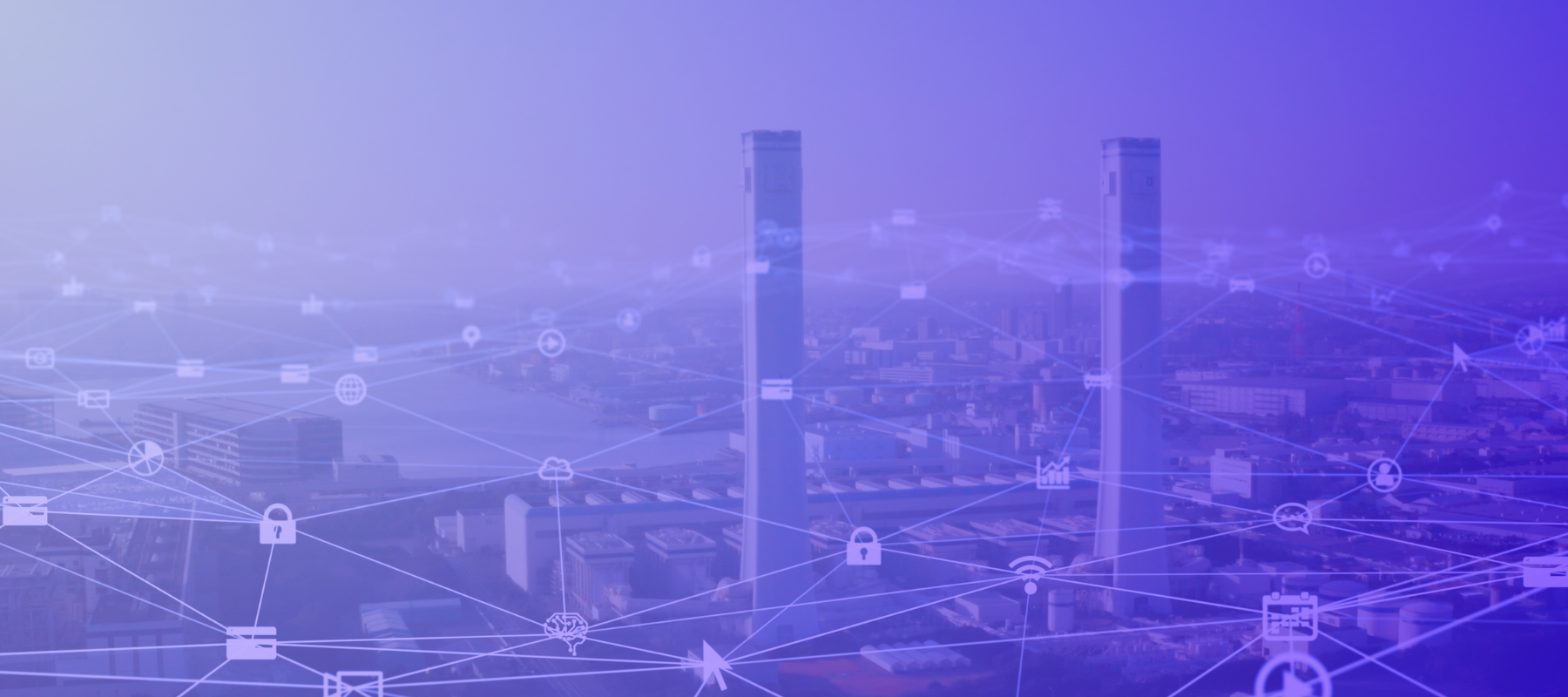
Electrical engineering is a large-scale industry that requires precision and high productivity. And to meet these demands, more and more manufacturers are turning to automation and relying on digital design tools when possible.
This shift to automation, however, isn't just a passing trend but a significant transformation affecting various production aspects.
In general, automation in electrical manufacturing has come a long way, especially with the advent of programmable logic controllers (PLCs) in the 1960s. Recent advances in robotics, artificial intelligence (AI), machine learning (ML), and the Internet of Things (IoT) have accelerated this evolution, bringing unprecedented opportunities and benefits.
Here's a closer look at how automation fits into electrical manufacturing — with examples, data, and real-world applications — and how TalentNeuron solutions can help.
Overview of Electrical Manufacturing Automation
Automation in electrical engineering is the application of technology to automatically improve and optimize the production processes for printed circuit boards, transformers, cables, electrical equipment, and other electrical devices and systems. In this industry, automation means combining sophisticated software, robots, and control systems to perform operations that were previously performed manually.
Current state of the electrical manufacturing
Automation technology is causing a revolution in the electrical manufacturing sector, leading to:
- Increased productivity. Automation has significantly enhanced manufacturing efficiency by cutting expenses and production times. This allows businesses to increase output and satisfy growing demand.
- Improvement of quality. Automated systems reduce human error and offer precise control over industrial processes, ensuring consistent and high-quality output. Adopting automation tools, such as generative AI and process intelligence, helps improve quality control and streamline operations.
- Dynamics of labor. Automated systems decrease the need for physical labor but also increase the need for specialized individuals to operate and maintain them. As a result, there are more opportunities to upskill and reskill workforces to become more tech-savvy.
- Supply chain optimization. Automation shortens lead times and boosts overall supply chain efficiency by facilitating real-time tracking and inventory management.
- Energy efficiency and sustainability. Automated systems are made to maximize energy efficiency, minimize waste, and support environmentally friendly production methods. It lowers operating expenses and is in line with global sustainability standards.
- Adoption worldwide. Nations with highly developed manufacturing industries — including the United States, Japan, and Germany are setting the standard for automation adoption. Emerging economies are likewise progressively incorporating automation to stay competitive.
Efficiency with Automation
Efficiency is a primary driver for automation in electrical manufacturing. Automated systems can perform repetitive tasks with precision and speed, reducing the time and labor required for production.
Why automate electronics manufacturing?
Electronics manufacturing is becoming increasingly complex as the size of components and circuits continue to shrink. High component density, small pitches, multiple layers, and small and delicate parts that require precise placement are just a few of the issues manufacturers encounter when building products.
Such issues are likely to introduce challenges that can slow down product assembly and testing. Also, the delicate nature of the circuits requires extra care, though errors, wastage, and inefficiencies are still likely to occur. As competition increases and demand for new features and products grows, manufacturers should look for innovative and efficient ways to do this.
Generally, automation improves processes and product quality while lowering operational and production costs, which is why the industrial automation market is expected to reach $395 billion by 2029. When implemented well, this translates to lower production costs, which manufacturers can pass on to their customers.
Robotic automation applies to almost all the stages in the electronics production cycle. The major areas are material and component handling, assembly lines, etching, inspections, testing, and more. Since most of these are repetitive tasks, robots can significantly reduce labor costs by reducing the number of employees while increasing production times and reducing errors and wastage.
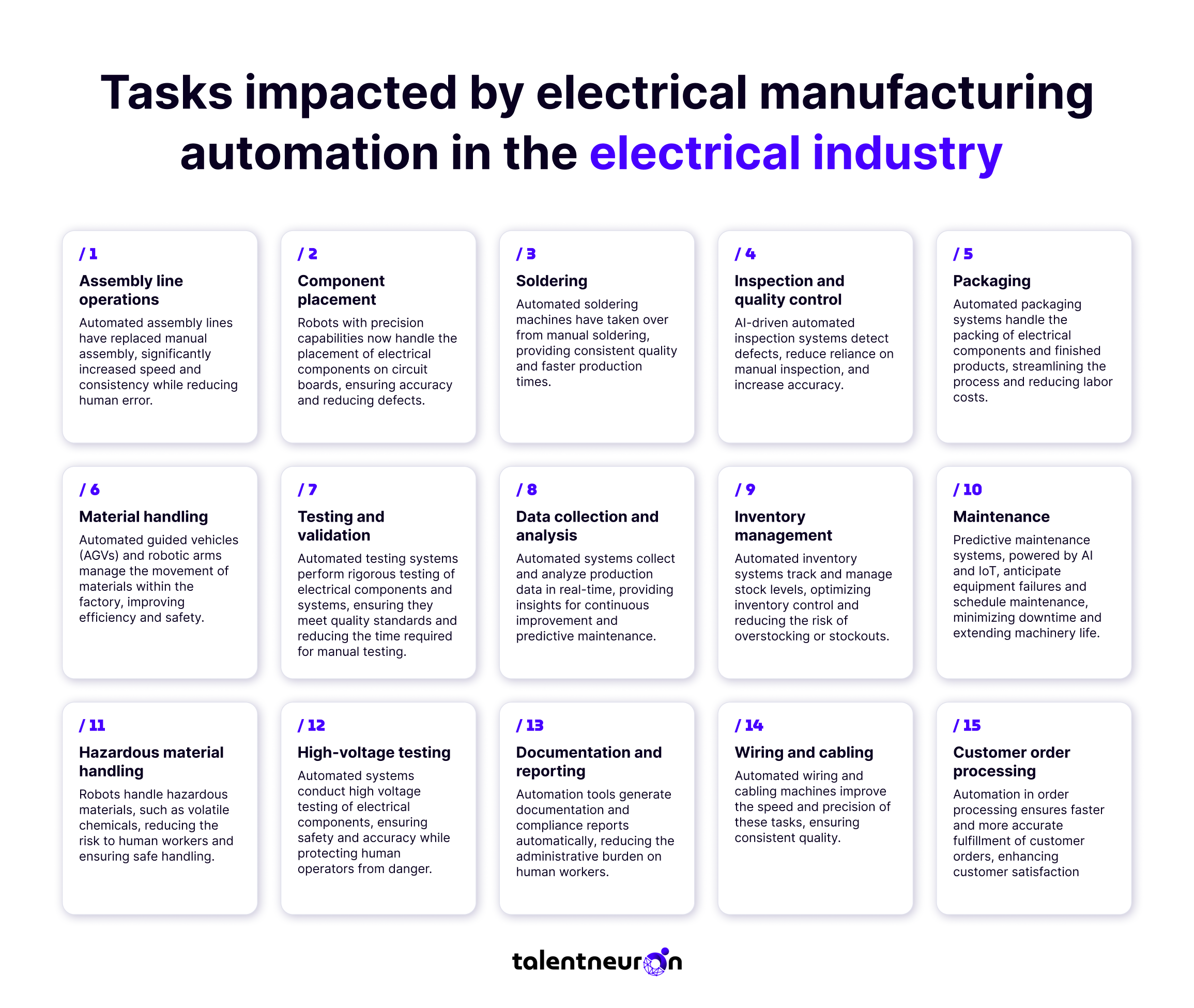
Automation Examples in Electronics Manufacturing
Assembly line automation
A prominent example is the automation of assembly lines. Robots with vision systems can easily assemble electrical components, significantly reducing assembly time. This can greatly increase production time and energy efficiency, according to a study by the International Federation of Robotics (IFR).
Automated inspection systems
Automated inspection systems, utilizing AI and machine vision, can detect defects in electrical components with a precision unattainable by human inspectors. These systems can identify minute flaws, such as micro-cracks or soldering defects, ensuring that only high-quality products reach the market.
Hazardous material handling
Robots can handle hazardous materials — such as volatile chemicals used in producing electrical components — reducing the risk of accidents. Automated systems can also perform tasks in dangerous environments, including high-voltage testing, ensuring human workers are not exposed to potential harm.
The Future of Automation in Electrical Manufacturing
The future of automation in electrical manufacturing is promising, with emerging technologies poised to revolutionize the industry further in the following ways:
- Artificial intelligence and machine learning: AI and ML are set to revolutionize predictive maintenance in manufacturing. By analyzing vast amounts of data, these technologies can predict equipment failures before they occur, thus minimizing downtime and enhancing productivity. For instance, AI-powered predictive maintenance can significantly reduce unplanned downtime and decrease maintenance costs by up to 10%.
- Collaborative robots (cobots): Cobots are designed to work alongside human workers, combining the precision of robots with the flexibility of human labor. These robots improve efficiency in tasks requiring a delicate touch or intricate assembly without replacing human workers.
- Internet of Things: IoT devices create a smart manufacturing environment by connecting machines, sensors, and systems. This connectivity allows for real-time monitoring and control of production processes, enhancing efficiency, quality, and safety. With IoT-enabled sensors, operation teams can detect anomalies early and enable proactive maintenance, significantly reducing equipment failure rates and maintenance costs.
But benefiting from these advancements takes more than just acquiring the latest and greatest software and hardware — organizations also need a workforce that's ready for automated workplaces, too.
TalentNeuron is at the forefront to strategic workforce planning and transformation, providing the data-backed insights and tools needed to navigate this future. Drawing on 33 terabytes' worth of data collected from more than 28,000 diverse sources, TalentNeuron solutions help businesses explore roles and skills that are critical for current and future workforce needs — including automation.
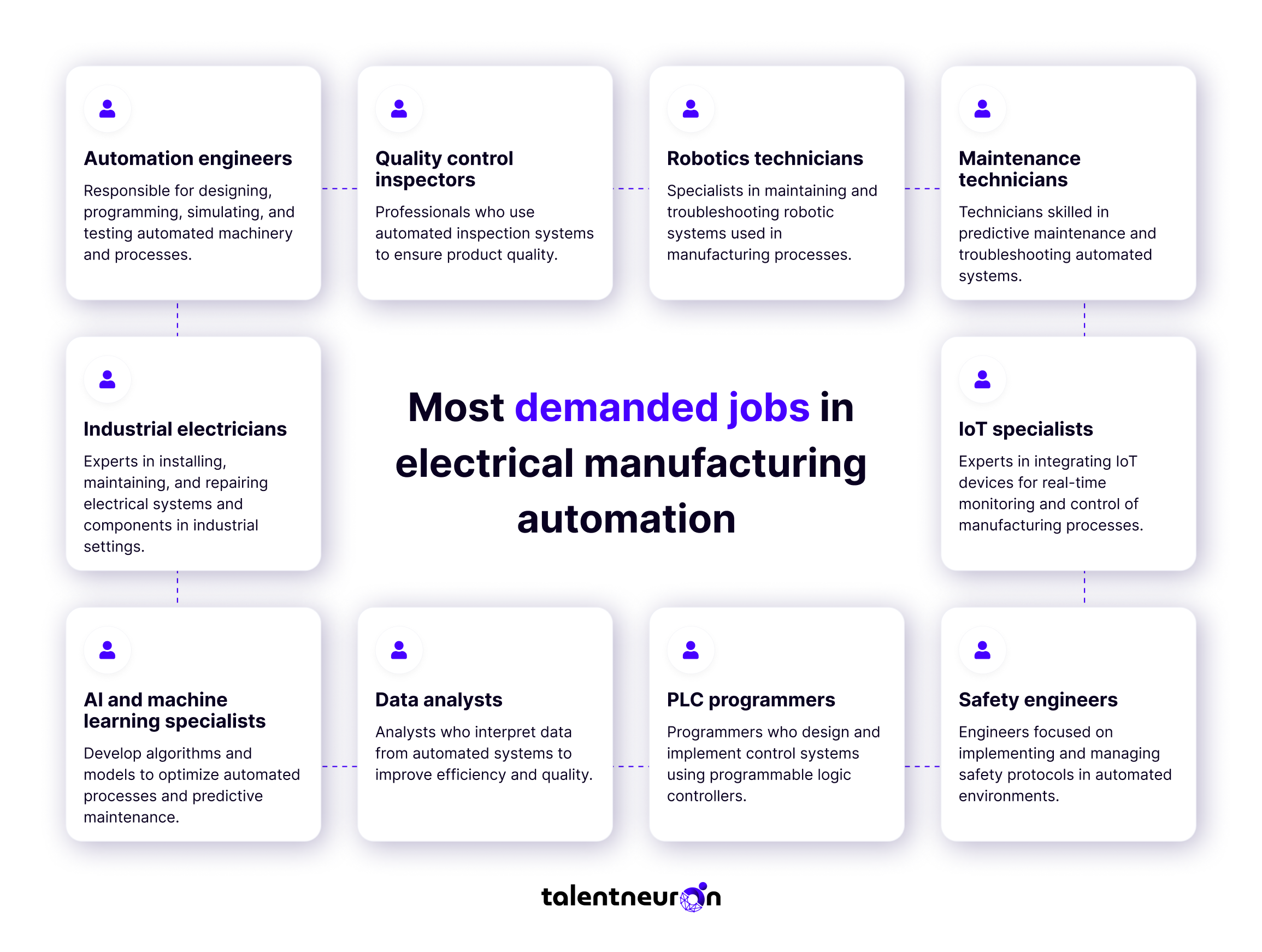
With real-time visibility into job demand and skill evolutions, HR teams can identify existing workforce gaps and make build-borrow-buy decisions on talent that can effectively build and maintain automated workplaces in electrical manufacturing and other industries.
.gif)